Built by hand. Backed by heritage.
If you’re a retailer looking for quality that sells and a supplier you can count on, here’s what sets our hats—and our artisans—apart.
At Master Hatters of Texas, every hat is shaped with intention, finished by hand, and crafted under one roof in Garland.
We use the kind of equipment that’s earned its place in the trade—presses, and forms that help keep things precise—but what gives an MHT hat its edge is the people behind it. The ones who know when to push steam, when to ease pressure, and when to trust their hands more than the machine.
This is what it looks like when you build something the right way. And still do.
1. Every Hat Starts with Purpose
No two orders are the same. Some retailers order straight from the catalog, while others come to us with private label plans or requests for custom touches that set their shelves apart.
What follows isn’t just production—it’s a system built over time with felt, tools, and hands that know how to work both. We don’t rush, but we do run a tight shop that understands timing matters.
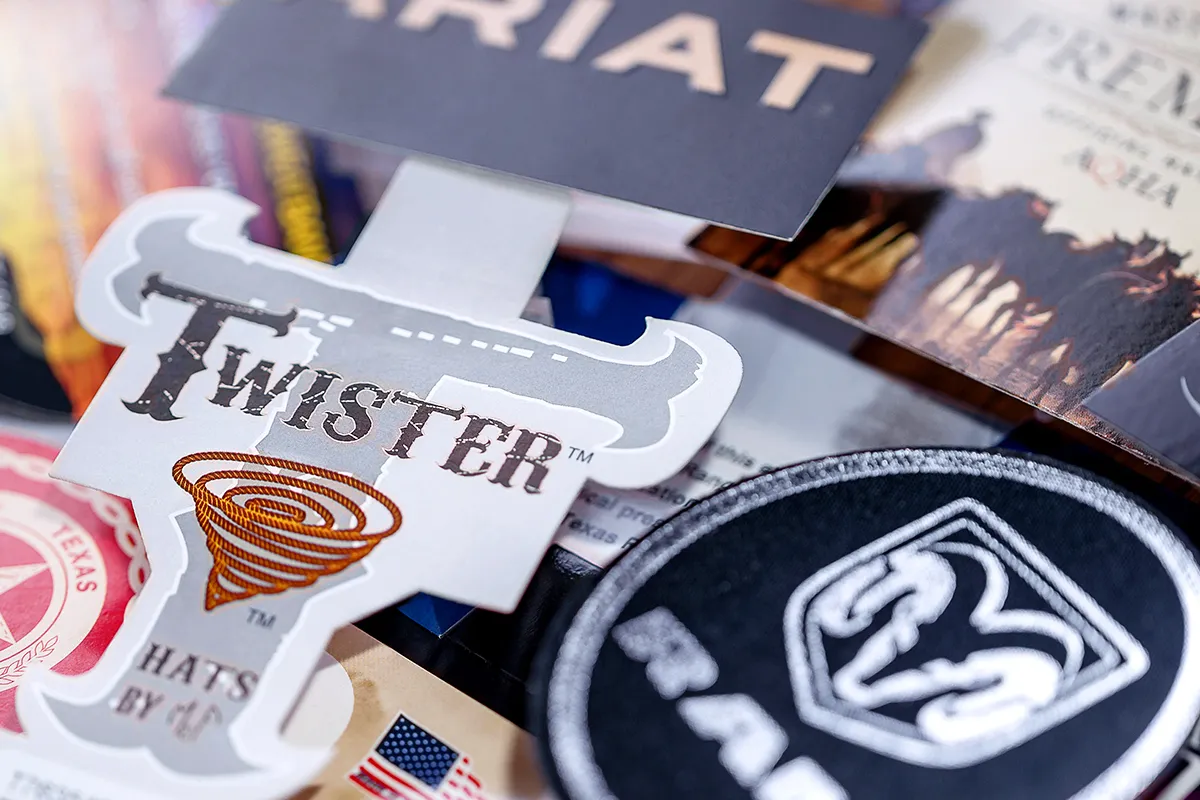
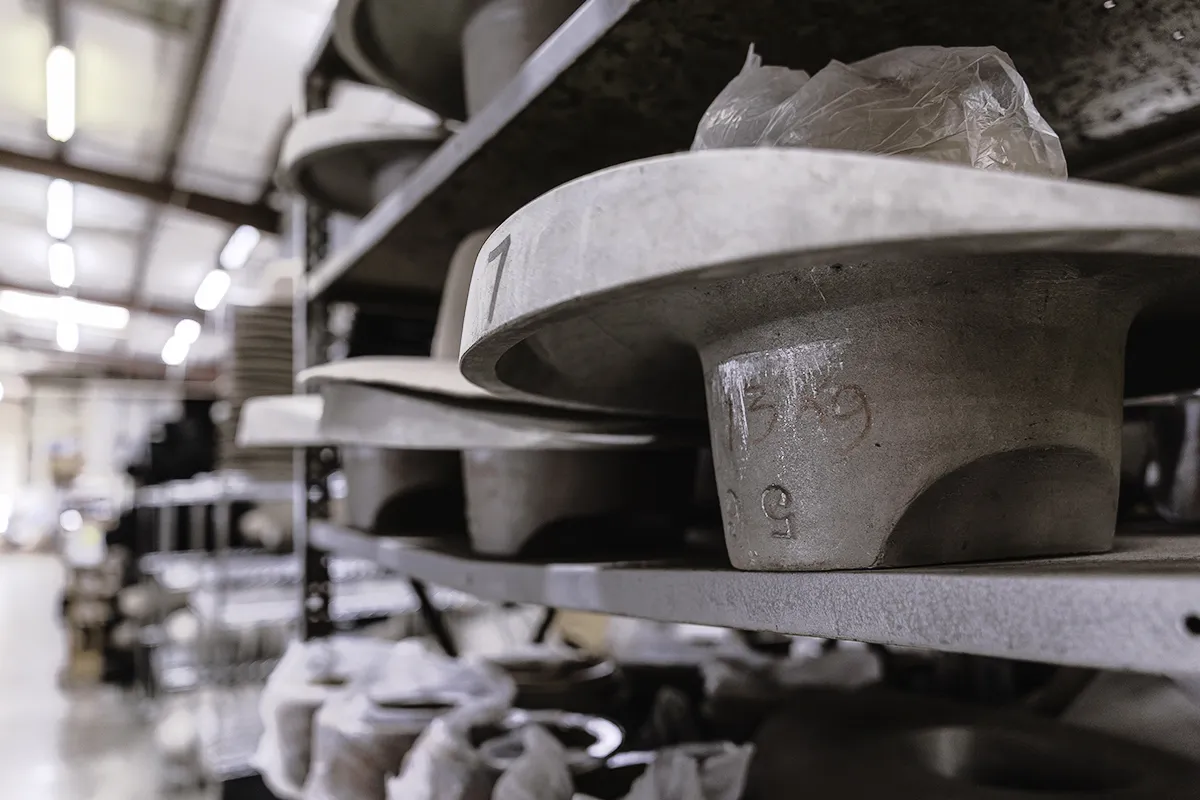
2. Shaping with Precision and Pride
There’s a rhythm to it—steam rising, hands turning felt, the weight of the press locking into place. We use shaping blocks, sure. But the true shaping happens when someone who’s done this a thousand times adjusts just a little more tension or leans in to make it right.
Crowns are formed with structure. Brims are set with weight. But the finishing? That comes from instinct—and a work ethic you can’t teach.
3. Stitch by Stitch, the Details Matter
This is the part most folks never see. The inside of the hat is where lining meets band, where foil hits leather, and where sweatbands are stitched in straight and snug.
It’s quiet work. Steady hands. Focused eyes. And that matters more than people think.
Private label partners get their mark placed here, tucked inside the crown or on the band. It’s a nod to where the brand is headed without forgetting where it started.
4. Final Touches That Make a Difference
Before anything leaves the shop, it’s brushed, checked, and boxed with care. No stockpile. No “close enough.” Just hats made to order—on time, on spec, and ready for the shelves.
We build with efficiency. But we never cut corners.
Why It Matters
These aren’t hats made to blend in. They’re made to hold up, stand out, and carry the mark of the hands that built them.
We use tools that help us move efficiently, but we don’t let machines take over. There’s a reason retailers keep coming back—and it has less to do with the process and more to do with the people shaping it.
Looking to place your next catalog or private label order? Let’s talk.
972-864-5523 / moc.srettahretsamobfsctd-314fae@ecivresremotsuc